

The
Industrial
Packaging
Association
Plastic Drums
Our members manufacture and supply a wide range of plastic drums and kegs
PLASTICS PACKAGING DESIGNED TO MEET THE FUTURE...
​
SERVING THE INDUSTRIAL SECTOR
Continuous development over the past 20 years in polymer, extrusion blow moulding and rotomoulding technologies, coupled with refinements in design concepts, has resulted in a range of plastics drums which meet the needs of various chemical industries and other industrial applications.
The plastics drum range has been developed to take into account issues relating to safety, handling and legislation.
Not only in respect of the transport of dangerous goods, but more recently issues relating to the environment with regard to packaging and packaging waste, thus embracing the main principles outlined in the EC Packaging and Packaging Waste Directive in respect of Reduction at source, Reuse, Recycling and Recovery.
​
DESIGN
-
Compatibility with specific industries logistics systems.
-
Ease of handling - both mechanical and manual.
-
Dispensing - easy to pour - adaptable for specific dispensing systems.
-
Colour and decoration for corporate image.
-
Low level of product residues which aides recycling and disposal.
​
TRANSPORT
Improved technology enables plastics drums to be manufactured in designs shaped for purposes. For example, optimum efficient pallet utilisation, Resulting in:
-
Significant reductions in storage, handling and distribution costs.
-
Higher payloads for transport by road and in ISO shipping containers, by up to 50% in certain new design cases when compared with round drums.
​
FILLING & EMPTYING
Plastics drums can be produced with a variety of closure systems to meet customer's specific requirements, including automatic filling lines. The malleability of plastics gives more flexibility in the design of the container than other processes and materials, which allows for total drainability of the contents, reducing waste and making recovery much more effective.
​
PERFORMANCE TESTING
Designed to meet the test criteria laid down in the UN Recommendations for the Transport of Dangerous Goods in respect of Drop, Stacking, Leakproofness and Internal Pressure tests, together with chemical compatibility in accordance with the RID/ADR European Rail and Road regulations concerning the International carriage of dangerous goods.
​
RECOVERY
HDPE is made from oil and contains a similar calorific value, which can be recovered in state of the art Energy from Waste or Power Furnaces to produce heat and electricity (only 4% of oil is used manufacturing all plastics).
​
RECYCLING
Plastics is an excellent material to recycle, as demonstrated by the growing end user markets for used plastics containers. Plastics Containers can be chipped, washed and turned into post-consumer recycle material (PCR), for use as raw material to manufacture non-food industrial and consumer Plastics Containers, PCR can also be used to produce both domestic and garden products - dustbins, composters, water butts etc. In the future, it will be possible to recycle plastics drums using innovative feedstock recycling technologies such as polymer cracking. Plymer cracking returns the plastics back into hydrocarbon feedstock from which new plastics and other products can be produced.
​
REUSE AND RE-CONDITIONING
Many industries are moving into the reuse concept, for which the plastics drum is ideally suited. Durability and robustness has enabled 'closed loop' systems to be established in the catering, institutional chemical, photographic, water treatment and crop protection industries. Plastic drums are also suitable for laundering using the traditional re-conditioning facilities. The multi-trip drum concept results in a reduction in packaging waste.

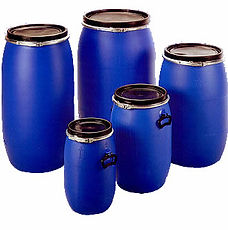
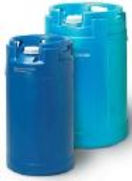

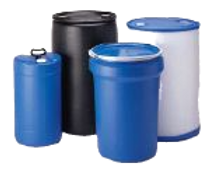

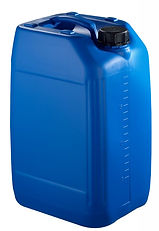